Восстановление подшипника за 1 час с помощью AWS.
- Главный по присадкам
- 1 сент. 2015 г.
- 4 мин. чтения
Противоизносные составы, на основе минералов природного происхождения, обладает уникальными свойствами. В процессе трения поверхностей трибосопряжения с привнесенными противоизносными составами формируется металлокерамический поверхностный слой. Это приводит к залечиванию усталостных микротрещин, микроповреждений поверхностей после механической обработки, устранению последствия разрушающего проявления водородного растрескивания и электрохимической коррозии и не допускают этого в будущем. В результате поднимается и выравнивается компрессия ДВС, увеличивается мощность, уменьшается расход ГСМ, увеличивается срок службы агрегатов и многое другое.
В данной статье мы рассмотрим, как противоизносные составы, на основе минералов природного происхождения, работают в подшипниках. Для того, что бы показать действие противоизносных составов и увидеть результат – проведём эксперимент в лаборатории трибологии. Для эксперимента был взят типичный подшипник №8202, который легко разбирается. Он выдерживает большие перегрузки, сделан из высоколегированной, инструментальной стали ШХ-15. В автотранспорте эта высококачественная сталь используется для производства нагруженных узлов, такие как ШРУСы, ролики толкателей, плунжеры насосов высокого давления и опорные подшипники валов КПП. Серийный подшипник № 8202 по ГОСТУ, производства 20 ГПЗ. Применяется в топливной системе дизельных ДВС тракторной техники, в червячных редукторах, шпиндельных узлах и др. С помощью гравёрной фрезы делаем повреждения на дорожке качения нашего экспериментального подшипника (см. рис.3), т.е. осознанно повреждаем часть плоскости. Высверливаем, царапаем в значительной степени, для большей наглядности изъяны моделируются «с запасом», в несколько раз опасней тех, которые могут показаться на плоскости при настоящей эксплуатации. Затем закладываем смазку (0,5 мл). Носителем противоизносных составов, на основе минералов природного происхождения, в данном эксперименте выступает смазка НТ, созданная для узлов с большим (до 80 %) износом. Начинаем «крутить» подшипник со смазкой на особой установке под большой нагрузкой (8000 Н и 1000 оборотов в минуту) не останавливая, что близко к режиму штатной эксплуатации. В период данной работы происходит формирование металлокерамического защитного слоя на плоскости трения в виде металло-матричного нанокомпозита, причем в период приработки осуществляются процессы изоморфизма, в результате которых происходит глубокая диффузия замещенных структур в матрице основного металла в виде ассоциатов ортогонально поверхности трения. Процесс формирования металлокерамического защитного слоя происходит быстро, через 15 мин. работы, пока ещё видны очертания повреждения, приостанавливаем работу установки. Посмотрим, что же произошло с поверхностью дорожки качения. Работу подшипника под перегрузкой гарантирует специальная установка, которая позволяет оценить уровень ремонтных, восстановительных и защитных параметров противоизносных составов, на основе минералов природного происхождения.

Рис. 3. Часть дорожки подшипника.
Начальная фабричная плоскость шершавая, с глубокими отпечатками от шлифовального прибора. По центру – точечный недостаток (кратер, каверна), объемом более 0,5 мм в поперечнике и глубиной до 0,7 мм, который мы специально сделали гравёрной фрезой для эксперимента.

Рис. 4. Тот же участок дорожки подшипника после 15 мин. работы под нагрузкой. Плоскость зеркальная, гладкая. Отпечатки от фабричной шлифовки отсутствуют. Видно очертание кратера, хорошо заметно, какое количество за это время наросло металлокерамического слоя.
Даже невооруженным взглядом заметно, сделанное нами, повреждение значительно стало меньше, затянулось с краев. Фото с микроскопа (рис. 3 и 4) позволяют осмотреть составные части – небольшие отпечатки от фабричной шлифовки за это время скрылись, у края кратера возникли наплывы. Схематично действие противоизносных составов показано на рисунках 3и 4. Хорошо видно, что увеличение металлокерамического слоя происходит на краях кратера, со временем наполняя повреждение от краев к центру.
Мы подошли к основной части нашего эксперимента. Наращивание металлокерамического защитного слоя происходит в парах трибосопряжения различных узлов и агрегатов в режиме штатной эксплуатации. Он как бы возвышается над поверхностями трения, что дает возможность сгладить их микрорельеф. Позволяет вернуть исходную геометрию изношенных поверхностей трения, компенсируя собой износ. При этом происходит оптимизация зазоров, что называется «по факту сборки» и по фактическому износу. Оптимизация приводит к снижению вибраций, локальных перегревов, что является одним из факторов экономии энергоресурсов. Толщины слоев различны и зависят от степени разрушения сопряженных поверхностей трения. Проанализируем, как появляется повреждение на настоящих элементах ДВС. Чтобы получить износ достаточно царапины, либо скола от жестких частиц (пыли, грязи, мелких опилок, стружки). На их месте появляется зона ненормальной поверхностной активности. Атомы металла тут имеют некомпенсированные взаимосвязи, и, при повышении перегрузки, их с легкостью «раскачать» и оторвать от матрицы. Металл начинает уходить в стружку. Повреждение увеличивается и происходит износ элементов. Что бы осознать значение данного процесса, достаточно понять – в 4 литрах отслужившего масла находится около 2 грамм металла. А капитальный ремонт делают при износе не более чем 60 граммов метала для ДВС объёмом 1800 см3. На первый взгляд может показаться, что 60 грамм металла для 100-килограммового ДВС – просто капля в море. Но беда в том, что износ происходит в основных парах трения (кольцо – цилиндр, шейки вала – вкладыш и так далее), которые отвечают за работу и параметры ДВС. Результаты такого износа для ДВС прогнозируемы и пренеприятны: в таких случаях уменьшается мощность, уменьшается компрессия, это ведет к увеличению расхода ГСМ, повышение содержания вредных соединений в выхлопных газах. Надо отметить, что, падение компрессии на 20-25 %, к примеру с 14 до 10 единиц, говорит о 100 % износе ДВС по тех. данным заводов-изготовителей. Плохим сигналом о нарушении работы ДВС служит разброс компрессии по цилиндрам более 2 единиц для дизельных агрегатов и 1 единицы для бензиновых агрегатов, расход масла больший, нежели 0,4-0,6 % от расхода горючего (т. е. 0,8 литра на 1000 км при расходе горючего 10 литров на 100 км). Данный эксперимент – наглядная иллюстрация к тому, как действуют в процессе восстановления противоизносные составы, на основе минералов природного происхождения.

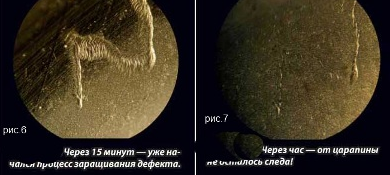
Процесс восстановления виден уже через первые 15 минут, металлокерамический защитный слой формируется на поверхности дорожки подшипника и идёт заращивание дефекта (рис. 4 и 6). Через 1 час от царапины не осталось следа (рис. 7), дефект устранён. При применении противоизносных составов, на основе минералов природного происхождения, значительную долю эффекта снижения трения и износа дают специфические механические характеристики этих материалов и строение их электронных оболочек. Результаты применения противоизносных составов в качестве тонкослойных покрытий на деталях пар трения основных существующих в технике групп машин и механизмов, показали, что с применением данного метода механические системы выходят на качественно новый уровень, резко, в некоторых случаях в 20 – 30 раз, снижая величину механических потерь и интенсивность изнашивания узлов. Некоторые типовые механизмы и машины после применения выглядят следующим образом:
механический КПД автомобильного двигателя в целом увеличивается с 0,74-0,83 до 0,98-0,99; межремонтные периоды увеличиваются в 4-5 раз; потребление смазочных масел снижается минимум в 2-3 раза; двигатель получает возможность работать без подвода смазки, имея лишь тонкую плёнку масла на поверхности трущихся деталей;
воздушные компрессоры получают механический кпд 0,98-0,99;
турбокомпрессоры большой мощности (10 МВт) уменьшают свои механические потери с 10% до 1-2% и объём необходимых регламентных работ у них сокращается в 2,5 раза;
зубчатые передачи снижают интенсивность изнашивания в 40-60 раз;
трудоёмкость изготовления отдельных деталей снижается в 5 раз при улучшении их триботехнических характеристик;
станочный парк снижает энергопотребление в среднем на 15%, появляется возможность восстановления изношенных узлов без вывода станков из эксплуатации.
Commentaires